Industrial Design | Product Strategies | Design Management

Halcyon
Biomaterial Research & Regenerative Prototyping
Halcyon is a material exploration project rooted in ecological intelligence — where design meets climate-conscious production. Developed during my MFA at Parsons, the project centers on creating 3D-printable filaments from biodegradable sources, inviting a new way of thinking about digital making: one that regenerates instead of extracts.
Regenerative Design
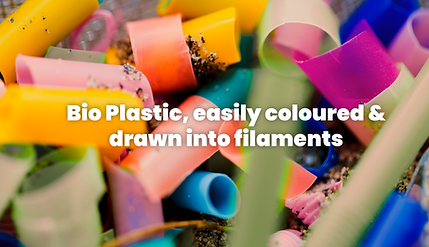
Systems Thinking
Halcyon isn’t just about a single material — it’s about designing a regenerative system. How might biodegradable objects be locally fabricated and composted?
What if supply chains were seasonal?
The project becomes a provocation:
What does sustainable prototyping actually look like when we stop centering petroleum?
Key Goals
-
Manufacture recyclable, compostable objects
-
Replace fossil-based industrial plastics
-
Demonstrate a closed-loop fabrication system
Prototype Insights
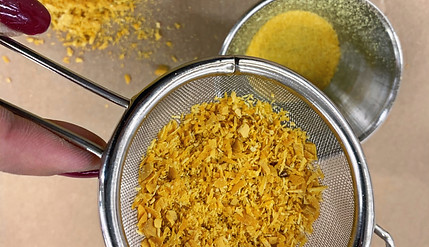
Halcyon — Regenerative Prototyping & Insights
Material Ideation & Biopolymer Selection
Surveyed existing bioplastics and conducted early-stage experiments with agar, starch, cellulose, and lacquer. Identified lacquer for its historic durability, moldability, and natural polymer behavior.
Composite Formulation
Developed lacquer-beeswax composites to improve ductility and thermal performance. Ran melting point tests to identify optimal blend ratios for printability and structural integrity.
The resulting material was not only biodegradable, but capable of fine detail and reusability — supporting both recyclability and aesthetics.
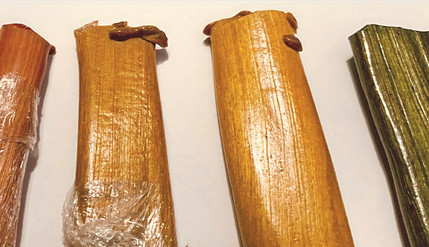
Lacquer as a 3D Filament
Raw lac, harvested from lac insects living on forest trees, was reimagined into a bio-composite. Through hundreds of iterative tests, I developed a formula combining lacquer and beeswax, where beeswax provided ductility, enabling the composite to be extruded into 1.5mm filament compatible with FDM printers.
Halcyon challenges the norms of digital making by exploring organic material languages — soft, impermanent, and alive. Instead of mimicking petroleum plastics,
Temperature Study

Material Behavior & Temperature Study
A core phase of Halcyon involved intensive material testing to understand lacquer’s thermal behavior and compatibility with extrusion-based 3D printing.
Through controlled melting trials, I charted lacquer’s transition phases — from softening to flow — identifying the optimal temperature range for stable extrusion without carbonization or structural failure.
To balance brittleness and enhance flexibility, beeswax was introduced as a plasticizer, creating a composite that could hold form under low-heat conditions.
Material Behavior

Prototyping Process
Experimented with ratios of lacquer and natural binders
Each iteration was tested for:
-
Melting point stability
-
Viscosity and flow rate during extrusion
-
Surface finish post-print
-
Cooling and solidification time
Printer Modification
Adapted an FDM printer and extruder to handle composite material. This versatility emphasized the material’s potential not just for digital prototyping, but also for low-tech, localized fabrication methods. This data directly informed the design of a custom extruder head and print temperature profile, tailored to the lacquer–beeswax filament's behavior.
Circular Material

Toward a Circular Material Future
The goal of Halcyon is to manufacture recyclable, compostable objects with near-zero waste — replacing fossil-based industrial plastics and shifting toward a circular design economy.
Through iterative testing, I developed a composite of lacquer and beeswax, where:
-
Beeswax introduced ductility and flexibility,
-
Lacquer provided a durable, printable base.
This unique blend enabled the creation of filaments compatible with FDM 3D printing — opening possibilities for biodegradable structures that retain strength while naturally decomposing.
Form Responsiveness

Moldability & Form Responsiveness
Beyond 3D Printing
I explored the moldable potential of lacquer-based composites. Once heated to their workable state, the materials could be poured, pressed, or hand-formed into molds without losing structural integrity.
-
The lacquer–beeswax blend displayed a slow curing window, offering time for manipulation and layering — enabling a range of techniques from casting to sculpting.
-
In doing so, Halcyon positioned moldability as a key characteristic of regenerative design — adaptable to both high-tech extrusion and handcrafted processes.
Technical Innovation

Technological Innovations
-
Custom filament extruder with CNC-milled hopper system.
-
Modified print bed and thermal controls for sensitive materials.
-
Integrated low-energy fabrication setup to reduce waste and emissions.
Technical Process
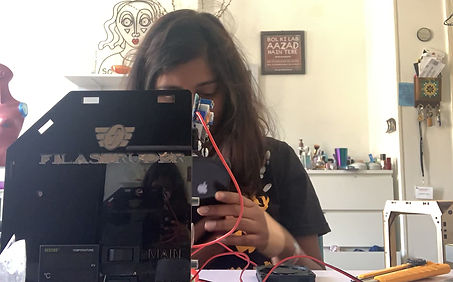
Extrusion & 3D Printing Trials
Built a custom extrusion setup for FDM compatibility. Iterated nozzle temperatures, cooling times, and feed rates to achieve smooth deposition. Assessed layer adhesion, print fidelity, and deformation.
Prototyping & Failure Studies
Produced small-scale speculative forms (e.g., vessels, architectural fragments) designed to fail or decompose. Observed changes over time to understand aging, compostability, and microbial breakdown.
Systems Mapping & Circular Feedback
Mapped a closed-loop system where printed waste re-enters the material supply. Explored seasonal, site-based fabrication models that support ecological rather than industrial rhythms.
Filament Success!

Material Properties Explored
-
Color & Finish: From deep red to light yellow, lacquer offered rich natural hues.
-
Form: Molded, extruded, and printed — lacquer's versatility supported shaping across scales.
-
Thermal Behavior: Precise melting point and cooling rates were studied to avoid clumping or cracking during extrusion.
Circular System

Circularity & Regeneration
At the heart of Halcyon is a commitment to material circularity.
Unlike traditional plastics, the lacquer-beeswax composite is fully biodegradable..
-
Once a form reaches the end of its useful life — whether printed, molded, or cast — it can be reheated, broken down, and remade into new material without losing core structural properties.
-
The material’s organic origin allows it to re-enter the natural ecosystem safely.
-
Excess or failed prints don’t become waste — they become feedstock, melted back into paste or filament.
As Halcyon, every object is a phase, not an endpoint.
This approach reframes prototyping not as a linear act of consumption, but as a cyclical practice of renewal — aligning production with seasonal, site-responsive rhythms.
Proof of Concept

Prototyping, Material Test and a Design Provocation.
Using the lacquer-beeswax filament, I printed a series of small-scale objects, like eyewear frames — to examine structural integrity,. These artifacts weren’t just functional trials but conceptual probes into how regenerative materials could shape future everyday forms.
Final renders were created to visualize scenarios highlighting the potential of bio-based materials across wearable product design contexts. The renderings serve as speculative projections, imagining a design future where materials return gracefully to the earth.